倉庫改善に取り組もう(下) ~物流品質向上と倉庫マネジメントの実行~
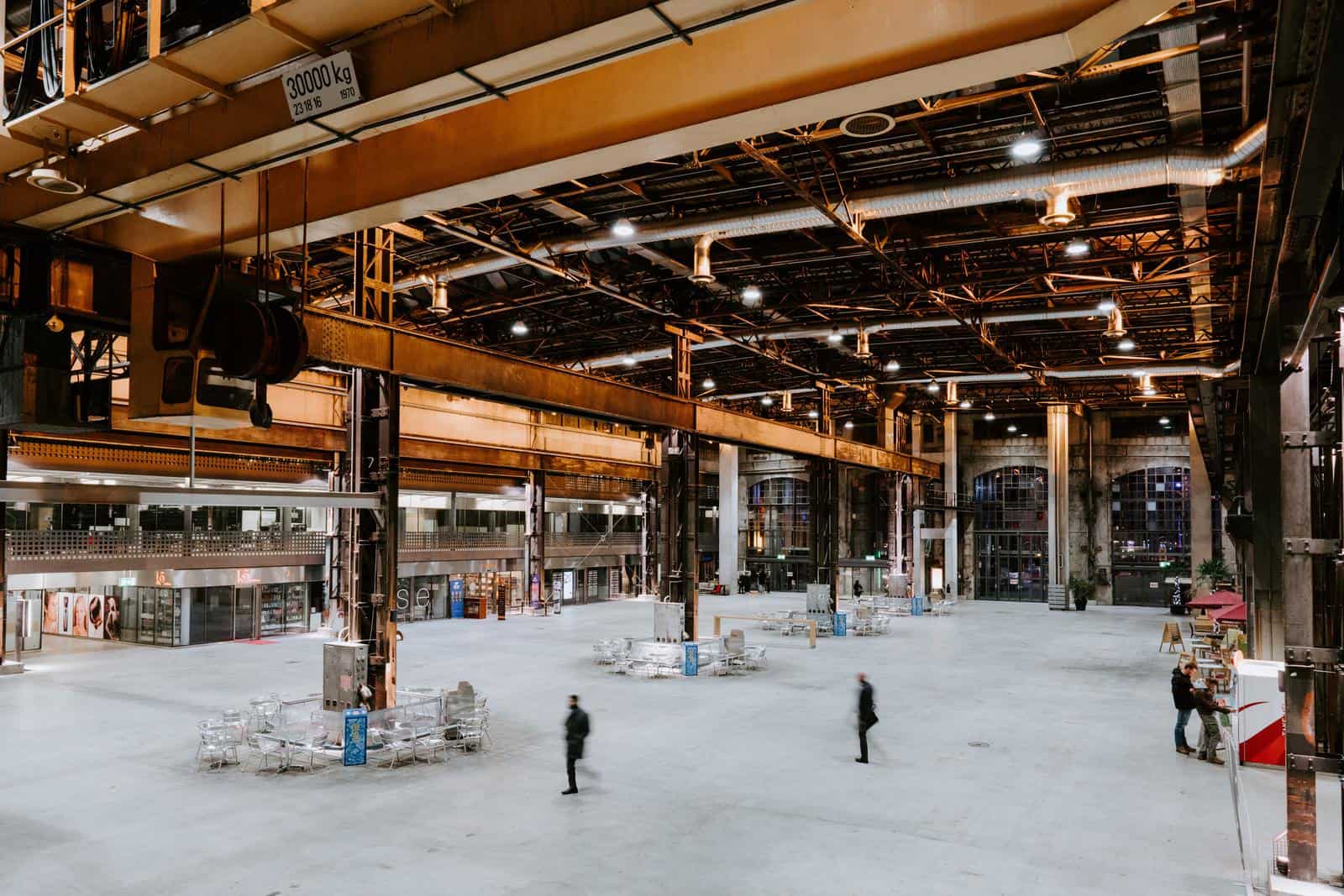
物流エラーを防ぐには
倉庫で間違いを防ぐためにはロケーション管理をしっかりとやることが重要。そのためには5Sをきっちりと行い、在庫管理の4原則を徹底し、社員教育を行っていくことが求められる。物流エラーは誤品や誤数、商品破損などが多いと思われる。これらの発生を防止するために上記に加えて行っていくべきことがある。
その第一ステップは標準作業の確立だ。当然のことだが標準作業がないと物流品質にばらつきが出る。なぜなら作業者ごとに仕事のやり方に差が出るからだ。作業者Aは慎重かつ丁寧に作業を行うためにエラーが少ないものの、作業者Bは雑な作業を行って間違いを多発する可能性がある。このようなケースで単純に監督者がBを叱るという行為を見かけるが、それは望ましくない。作業者Bが間違っているのではなく、「標準作業」を確立しなかった監督者が悪いのだ。標準作業が無いということは、作業のやり方を作業者に一任したということ。監督者には口出しする権利はない。
第二ステップは全作業者が標準作業を実施していることを確認することだ。よく標準作業を作ってもその通りに作業が行われているか確認していない会社がある。というか、標準作業の確認を行っていない会社の方が多いかもしれない。標準作業が行われているかどうかを確認することを「作業観察」と言う。現場の管理監督者の重要な仕事の一つがこの作業観察だ。標準作業書を持って現場に立ち、作業者の作業の様子を確認する。
ピッキング作業では作業者が「三点照合」を行っているかどうかに注目することが多いと思われる(図1)。もしこの三点照合を標準作業書に記述している場合、作業者がこのプロセスをカットすることは許されないからだ。
この二つのステップを確実に行っていれば物流エラーが発生する確率は極めて低くなると考えられる。
標準作業の中に作業者を交代して「ダブルチェック」を行うことを記述している会社がある。ダブルチェックを行っていても100%エラーが防げるかというとそうでもなさそうだ。何故だろう。それは同じような作業を毎日繰り返していると作業そのものがマンネリ化してくるからだと考えられる。ダブルチェックはいわゆる検査業務。しかし検査そのものにもマンネリ化は発生する。つまり検査しているつもりになってしまい、実際には見るべきポイントを見ていないということだ。ではこの状況を改善するためにはどうしたらよいだろうか。
意地悪チェックの導入
前述した通り、出荷品についてピッキング後にダブルチェックを行っている会社は多い。ダブルチェックの基本は人を入れ替えて実施するだ。しかしダブルチェックを行っても物流不良が顧客まで流出してしまうことがある。これはトリプルチェックを行っても同様。
もちろん、検査回数を増やせば不良流出の確率が低くなることは間違いないかもしれない。しかしなかなか「ゼロ」にはならない。何故だろうか。それは検査行為自体がマンネリ化し、検査の体をなしていないからだ。ダブルチェックを行う作業者が検査をしたつもりでも実際にはそれが検査になっていないのだ。
・ 納入ラベルと現物を照合する
・ 現物とピッキングリストを照合する
・ 納入ラベルとピッキングリストを照合する
・ 現物の正確性を確認するためにサンプルと照合する
このようなチェック方法があると思われる。このいずれかがおろそかになると物流エラーが発生する可能性がある。
そこでマンネリ化を防ぎ、確実な品質確認を実施するために「意地悪チェック」を導入することをお勧めする(図2)。意地悪チェックとは、ピッキングが終わった商品、ラベル、納品書のいずれかをわざとエラー状態にして検査者がそれに気づくかどうかを調査すること。たとえば商品Kを20個ピッキングしたものから「1個抜いて19個の状態を作り」それに気づくかどうかを調べてみる。
真剣に確認をしていれば当然気づくが、いい加減な仕事をしていればそのまま出荷してしまうことがあるだろう。また、商品Kをそれに酷似した商品Lに入れ替え、「誤品」であることに気づくかどうかの調査を行う。この時も同様にいい加減な確認では気づかない可能性があるのだ。
この「意地悪チェック」は現場で一定の緊張感を保つこと、物流不良の検出力を高めることが目的だ。あらかじめ抜き打ちで行うことを作業者に知らせておくことも重要。このような事前情報を流すだけでも物流エラーが減る可能性がある。なぜならいつ上司から見られているかわからないと意識することになるからだ。それだけでも緊張感が高まるだろう。
標準作業の確立、作業観察の実施をまずは確実に実施しよう。その上で意地悪チェックを導入することで物流不良は大幅に減少するものと思われる。
SQDCMマネジメントの実施
効率的かつ収益性の高い仕事を実現していくためには物流倉庫におけるマネジメントは重要なファクターになる。筆者が気になること。それは物流倉庫のマネージャーはどちらかというと現場のマネジメントについて十分な勉強ができていないということだ。そこで必要な管理を実体験させることで倉庫マネジメントの実施とスキル向上の両方が実現できることになる。
では倉庫マネジメントとは何なのか。倉庫マネジメントは5つの領域を管理していくことにある。それはSQDCM、つまり安全、品質、納期、コスト、マネジメントの5つだ。これらについて管理指標を設けてしっかりと管理できていることが収益向上につながる。
物流倉庫内で事故が起きていないか、事故を起こさないための活動が行われているのか、それらを数値化して管理していくことが重要。
品質については、誤出荷や商品破損が何件起きているのか、それを防ぐための対策をどれくらい打っているのかについての指標が必要。
納期については荷揃え遅れや出荷遅れがどれくらいあったのか、各工程の仕事が遅れないあるいは早すぎないようにどのような手段を講じているか、数字で示す必要がある。
コスト管理においては目標利益が出ているか、そのための一人一時間あたりピッキング件数や一人一時間あたり運搬量などの労働生産性がきちんと達成されているかを確認できるようにしておきたいものだ。
物流倉庫のマネジメトは特に現場で行っていくことが大切。泥臭いやり方かもしれないが、現場に管理ボード(図3)を設け、管理グラフを貼り出して全員でその情報をシェアできるようにしていくと良いのではないだろうか。
倉庫改善が進んでいるかどうかは管理グラフで示していくと確認ができると思われる。小さな改善を積み上げながら作業を効率化することは重要。しかし作業量が減っただけで作業者が楽になった状態で止まってはいけない。単に手待ち時間が発生するだけだから。効果は必ず刈り取る必要がある。当然のことだが、意外と刈取りが実行できていない会社を見かける。改善後は「作業員を一人単位で抜く」こと。抜いた作業者は新事業に振り向ける。この実行が重要だ。
倉庫改善を実施し、それを効果として「収支上の実額減少」で実現することだ。結果として倉庫利益に反映されていることが必要。ぜひ日々の改善を継続できるように倉庫メンバー全員で努力していこう。
この記事の作者

仙石 惠一
・物流改革請負人。ロジスティクス・コンサルタント。物流専門の社会保険労務士。
・自動車メーカーでサプライチェーン構築や新工場物流設計、物流人財育成プログラム構築などを経験。
・著書 「みるみる効果が上がる! 製造業の輸送改善~物流コストを30%削減~」
・日刊工業新聞、月刊工場管理、月刊プレス技術など連載多数。
http://www.keinlogi.jp/ 無料メルマガ 「会社収益がみるみる向上する!1分でわかる物流コスト改善のツボ」 https://www.mag2.com/m/0001069860