ミスを撲滅したければコレをやれ!顧客のハートを射止めるための物流品質向上作戦!(下)
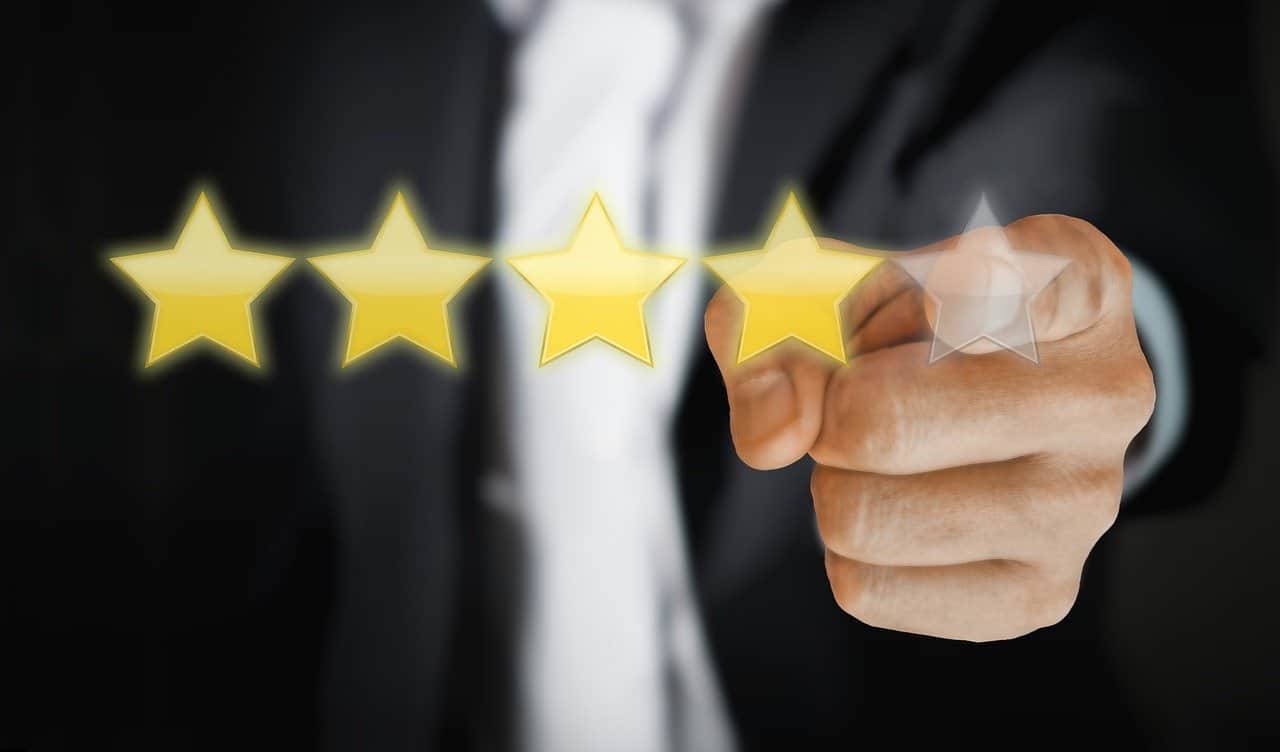
品質不良を発生させないための五ステップ
物流品質不良を発生させないために確実に実施していただきたいステップをご紹介しよう。最初のステップは「標準作業の確立」である。物流現場における仕事の進め方を手順で示すとともにその作業の「急所」を明確にする。すべての作業者にその手順で仕事を進めるように徹底することである。急所としては商品の確認ポイントや手で触れてはならない箇所などをきっちりと示すことである。間違いやすい類似商品がある場合にはその違いを写真などで比較して表示することが望ましい。
第二ステップが仕事の教え方である。仕事を教える際には「標準作業書」を使ってその通りにやって見せ、やらせて見せることが肝要である。
第三のステップは「作業観察」を行うことである。作業観察とは普段部下が標準作業通りに仕事をしているかどうかをチェックすることである。現場監督者の重要業務であり、毎日計画的に行っていくことが望ましい。もし標準作業と異なるやり方をしていたらその場で修正させる、これが第四ステップということになる。
この四ステップを行えば物流品質不良は激減できるはずである。不良を発生させた会社の要因分析を行うとこのいずれかが欠けていたことに気づく。特に「作業観察」を行っていなかったために仕事のやり方が標準作業から逸脱していたという話をよく聞くので注意が必要だ。(図1)
もしここまでのプロセスを100%実施しても物流不良が発生していたとしたらもう一ステップを追加しよう。これを第五ステップと呼ぶとする。ではこの第五ステップとは何か。それは「意地悪チェック」を行うことである。あまり聞き慣れない言葉かもしれないので解説しておこう。意地悪チェックとは棚の中に1個だけ酷似した別製品を入れたり、ピッキング後に1個製品を抜き取ったりして、作業者がそれに気づくかどうかをチェックすることである。やり方が意地悪いので意地悪チェックと言われる。(図2)
物流現場でダブルチェックを行っているつもりでも実質はブラインドになってしまい、見るべきポイントを見ていないことが多い。このチェックを行うことで作業者の不良検出力を向上させることができる。導入に際してはあらかじめ意地悪チェックを抜き打ちで実施すべき旨を作業者に説明しておく。作業者一人に対して月に一度は実施するように心がけたい。この事前告知が作業者の仕事に対する緊張度を高めることとなり、それだけでも、つまり実際に実施しなくても不良流出防止に役立つと思われる。
品質不良防止に向けての組織的取組
皆さんは多分お聞きになったことがあるだろうが「ハインリッヒの法則」というものがある。この法則は「一つの重大事故の背景には29の軽微な事故が存在し、さらにその背後には300の事故にいたらなかった異常が存在する」ということを示している。私たちが行っている物流作業の中にも多くのリスクの種が含まれているということを認識すべきなのだ。そこで物流品質不良を撲滅するために組織的な活動を行っていくことについて考えてみよう。先ほどの五ステップは物流現場監督者が中心に実施するがこれからの話は会社全体での取り組みとなることをご理解いただきたい。
第一に取り組むべきことは現場巡回の実施である。各物流現場を数名のチームで巡回しエラーが発生しやすいポイントを指摘していく。指摘された物流現場ではそれに対する改善策を打っていくことになる。このチームには他職場の管理監督者だけではなく、経理部門や営業部門など普段あまり物流作業に携わっていない人たちを参加させることをお勧めする。なぜならより新鮮な目で現場を見ることで問題に気づきやすいからである。
第二に取り組むことは小さなミスの報告制度の導入である。よく安全に関する取組の中でヒヤリハットメモを活用している会社は多いことだろう。このヒヤリハットを品質活動にも取り入れればよい。第三の取組は改善提案制度の導入である。物流品質向上に寄与する改善を実施しそれを報告する。報奨制度を設け、特に優れた改善事例に対しては報奨金を与えるとともに褒めるしくみを構築することが社員のモチベーション向上につながると考えられる。
品質不良が発生する背景にはモチベーション低下があると言われる。人がやることに間違いはつきものである。極力間違いを犯さないためにもモチベーション向上は欠かせないだろう。そして第四の取組としてQC活動の導入を挙げたい。何か品質上の問題が発生した場合にはその物流現場で課題解決のためのQC活動に取り組むことを心がけたい。QC活動の発展版としてQRQCという手法がある。このQRQCとは Quick Response Quality Control の略で「すぐに実施するQC」を意味する。物流品質不良あるいはそれにつながる問題が発生した際に、その日の終業時または翌日の朝に関係者で集まってその場で対応策の決定と実行のコミットメントを行うショートミーティングである。
最後に
物流品質は顧客にしてみればできて当たり前ととらえられがちであり、一般的に「当たり前品質」と言われる。しかし人間が行う作業である以上ミスはゼロにはなり得ない。ミスを極力ゼロに近づける努力をすることが物流現場に課されているのだ。よくお金をかけてポカ除け設備を導入することに頭が行きがちだが、その前に今回お示しした手順で現場の管理をしっかりと実行していただきたい。これができる会社を顧客は探しているということをご理解いただければ幸いである。
この記事の作者

仙石 惠一
・物流改革請負人。ロジスティクス・コンサルタント。物流専門の社会保険労務士。
・自動車メーカーでサプライチェーン構築や新工場物流設計、物流人財育成プログラム構築などを経験。
・著書 「みるみる効果が上がる! 製造業の輸送改善~物流コストを30%削減~」
・日刊工業新聞、月刊工場管理、月刊プレス技術など連載多数。
http://www.keinlogi.jp/ 無料メルマガ 「会社収益がみるみる向上する!1分でわかる物流コスト改善のツボ」 https://www.mag2.com/m/0001069860