倉庫改善に取り組もう(上) ~レイアウトとロケーション管理を工夫しよう~
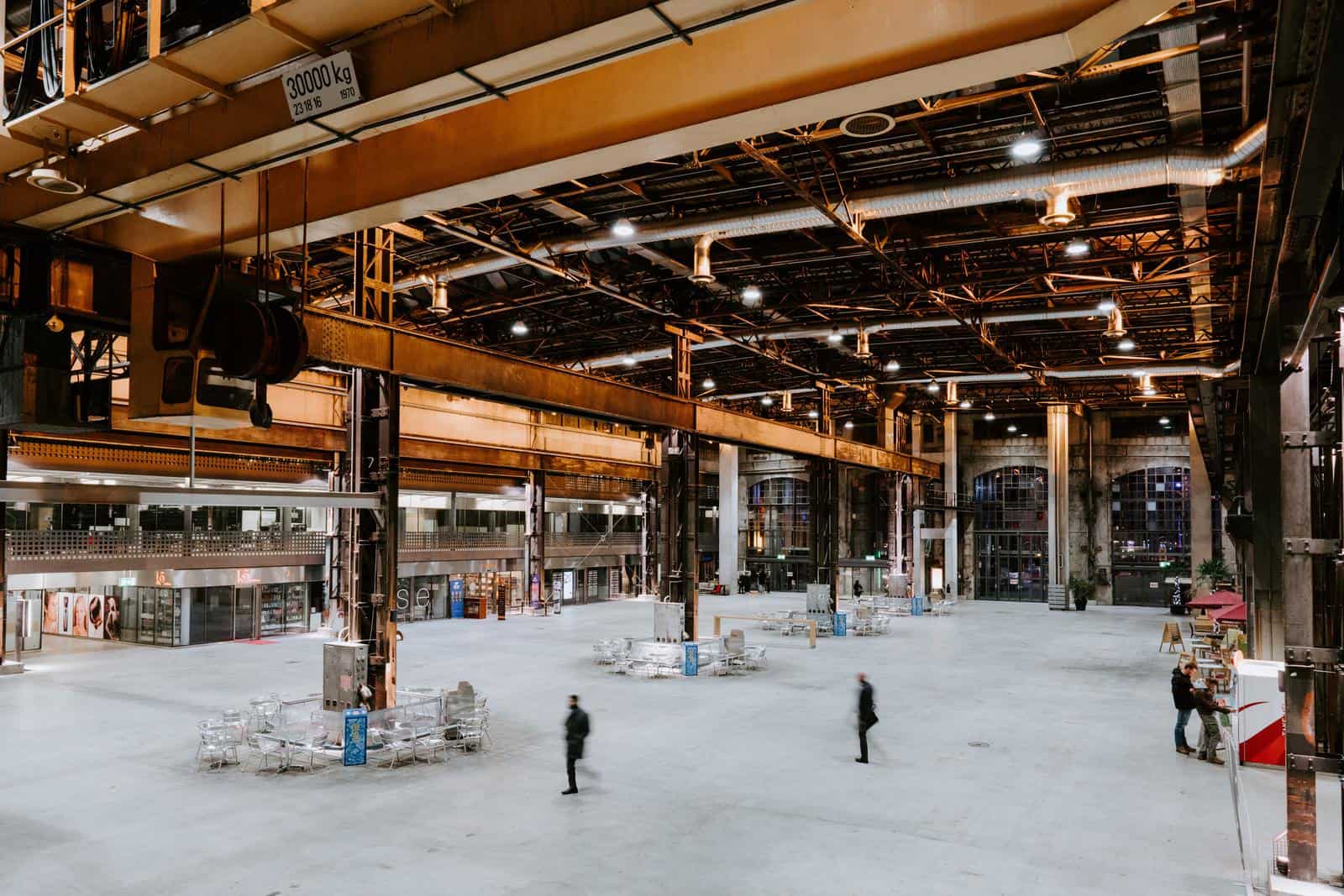
倉庫レイアウト改善
皆さんは普段使っている物流倉庫のレイアウトを改善したことはあるだろうか。物流効率はレイアウトに大きく左右される特徴がある。工程と工程が離れたレイアウト設計をすると永遠にその間の運搬が発生してしまうのはその一つの例だといえよう。
ではレイアウトをどのように改善していったらよいだろうか。その準備として工程分析を実施してみることをお勧めする。工程分析の結果、運搬や在庫の停滞が見える化される。今まであまり気にしていなかったような運搬や在庫がたちまち気になり出すことだろう。つまり今の隠れた問題点をいったん表化(おもてか)して認識することが今後のレイアウト改善を行う際に重要になるということだ。レイアウト設定時には良かったものの流れが、時代が経つとともに非効率になることも考えられる。物流量も当時と今とでは大きく異なることがあるからだ。そういった変化を放置していると、何となく効率が悪いなと認識しつつも仕事を続けることになる。やはり気づいた時に修正するという習慣が必要のようだ。
では早速倉庫レイアウトに必要な項目を挙げながら改善検討していこう(図1,2)。倉庫の建屋外にはトラックのポートや待機場が必要になる。トラックが物流倉庫に積み込みに行くと長時間待たされるという問題が発生している。この解消のためにはトラックダイヤ(図3)を定めるとともに荷揃えを行い、トラック荷役時間の低減が求められる。一般的にトラックドライバーは自分の積み込み時間より早めに到着することを考える。一方構外で待機されると近所迷惑となる。そこで一定のトラック待機場が必要になるのだ。
トラックポートの数も適正化したい。ある程度トラックが平準化される前提でポートの適正数を算出する。その数を物流倉庫に設置することになる。またトラックポートは屋根下に設置し、雨天時荷役への配慮を行う。トラックポート1つに1台ずつフォークリフトを配置する。その時のフォークリフト置場をレイアウトの中に設ける必要がある。もちろん、フォークリフトの燃料置場も忘れずに確保しよう。バッテリーフォークの場合には充電場所が必要だ。
荷受場と出荷場の改善
物流倉庫の荷受場、出荷場の改善は真っ先に取り組むべきエリアだ。この場所でものが詰まると清々とした物流を構築することはできないからだ。ここで重要となるキーワードは「わかりやすい」だろう。なぜならトラックドライバーや納入業者など外部の人たちが来て仕事をする場所でもあるからだ。外部の人たちが初めて来たときに迷わずに仕事ができるエリアづくりに努めたい。
たとえば出荷場であれば、トラックドライバーが積むべき荷物がすぐわかるようにしておくこと。そのためには「トラック単位の荷揃え」を行い、「納品書を準備」し、わかりやすい「表示」を設置しておくことが望ましい姿だ。荷受場であっても同様。どこに荷降ろしをしたらよいのかが瞬時に判断できるように大きな表示を付けておくようにしたい。そして2つの場所でともに改善しなければならないのがトラックポートと荷揃え場、荷降ろし場との間の距離だ。荷役時に長距離運搬が求められるとそれだけ時間がかかり、トラックの滞留時間を延ばしてしまう。荷降ろし時にあまりに多くの分散されたエリアに荷を仕分けて降ろすこともトラック滞留時間を延長させてしまうので注意が必要。
ポイントは「第三者の立場」で倉庫を見て判断すること。その意味で効果的だと思われるのは社内の、普段あまり現場と接点のない部署の人に倉庫を見てもらい、意見を聞いてみることだ。その人たちは倉庫という物流現場にとってはどちらかというと第三者に近いため、外部の人の意見に近いものが得られる可能性がある。
荷受場、出荷場でもう一つ気を配らなければならない場所がある。それは通箱(容器)とパレット(通箱等)の置場だ。通箱等は納入業者に返却する必要がある。またこれらは汎用的に活用が可能であるため、紛失防止のための管理も必要になる。時々特定の会社の名前が入ったパレットをその会社とまったく関係のない場所で見かけることがある。本来のルートから外れ、流出してしまった可能性があると考えられる。多くの会社で通箱等の流出(紛失)に悩んでいるようだ。しかしこれは会社における管理の仕方に問題があるととらえるべきだ。会社の資産管理をきちんと行うしくみは考えた方がよさそうだ。
ロケーション管理
物流倉庫内を改善する場合、ロケーション管理をしっかりと行っていきたい。この管理の精度によっては、誤出荷といった物流不良につながる可能性があったり、ものを探すなどの効率低下につながったりするので慎重に実施していこう。
ロケーション管理には「固定ロケーション」と「フリーロケーション」の2通りがある。前者はものの置き場所を固定する管理方法。列車で例えれば「指定席」だ。後者はものの置き場所を特定せず、その都度空いている場所に保管する方法。列車で例えれば「自由席」ということになる。両社ともにメリット、デメリットがある。固定ロケーションは場所が常に固定されているため置き場所がわかりやすく、新人作業者でもすぐに仕事をすることが可能。ただし商品の出方が変わったり廃止になったりした時に、置き場所に過不足が発生したりメンテナンスが必要になったりする。若干の煩わしさがあるかもしれないが、間違いを防ぐためには効果的な方法といえるだろう。
フリーロケーションは商品の出方が変わっても置き場所のメンテナンスは不要であり管理上は容易な方法だといえる。しかし都度置き場所が変わると倉庫内作業者の迷いが発生しがちだ。迷いによるロス時間、つまり探し回る時間がもったいないので、これをいかに防ぐか工夫が必要になる。愚直な改善方法にはなるが、2Sを徹底するとともに大きな看板をつけるとか倉庫内マップを掲示するなどの泥臭い手を打っていくことが効率化につながるだろう。
固定ロケーションの場合には、棚番号を「何丁目、何番地、何号」といった住所をイメージした数字とアルファベットを組み合わせた意味ありロケーションコードを基準化し付していこう(図4)。例えばAゾーンの01通路、右棚(R)11番の中段(Y)の場合は「A01R11Y」のようになる。
倉庫内のロケーションが定まったら、ピッキング作業にも大きな改善余地があるのでしっかりと効率化を進めていこう。
ピッキング作業者に発生させてはならない動作を挙げてみよう。
- 探す
- 開梱する
- 歩く
- 伸び上がる、屈む
- 手前の邪魔なものをどかす
- 商品を持ち変える、向きを変える
このような動作を発生させないように、ピッキング場の設計(棚の高さやものの置き方、通路幅や表示など)と作業指示の与え方を考慮することが重要。
よくピッキング用在庫とリザーブ用在庫を分離せずに同一場所保管しているケースを見かける。一番下の段はピッキング用、二段目から上がリザーブ用在庫として保管しているケースがその典型だ。このやり方だと通路幅が広がったり間口が大きすぎたりしてピッキング作業者の歩行を増やす要因となる。納入ロットと出荷ロットは異なることが大半なので、ピッキング場とリザーブ在庫保管場は分け、ピッキング効率を向上させることが望ましい。
この記事の作者

仙石 惠一
・物流改革請負人。ロジスティクス・コンサルタント。物流専門の社会保険労務士。
・自動車メーカーでサプライチェーン構築や新工場物流設計、物流人財育成プログラム構築などを経験。
・著書 「みるみる効果が上がる! 製造業の輸送改善~物流コストを30%削減~」
・日刊工業新聞、月刊工場管理、月刊プレス技術など連載多数。
http://www.keinlogi.jp/ 無料メルマガ 「会社収益がみるみる向上する!1分でわかる物流コスト改善のツボ」 https://www.mag2.com/m/0001069860